We provide OEM/ODM services, we have a professional team to help you realize them, you just follow these steps to get started:
Step 1: OEM communication
You have full control of the designs. We can put your logo on the products, and also accept customized packing box or other printing materials.
Step 2: Contract and Payment
Following mutual confirmation of order details, a pro forma invoice will be issued by us, you need to arrange the necessary down payment and return the duly signed pro forma invoice.
Step 3: Sample
The sample will be produced based on the confirmed design drawings, you need to confirm if the sample is acceptable.
Step 4: Bulk Manufacturing
We will start bulk manufacture according to the confirmed sample, and regular updates regarding the order production process will be provided to keep you informed.
Step 5: Booking & Shipping
We would like to book the cargo before bulk products finished and provide the bulk production photo before shipment.
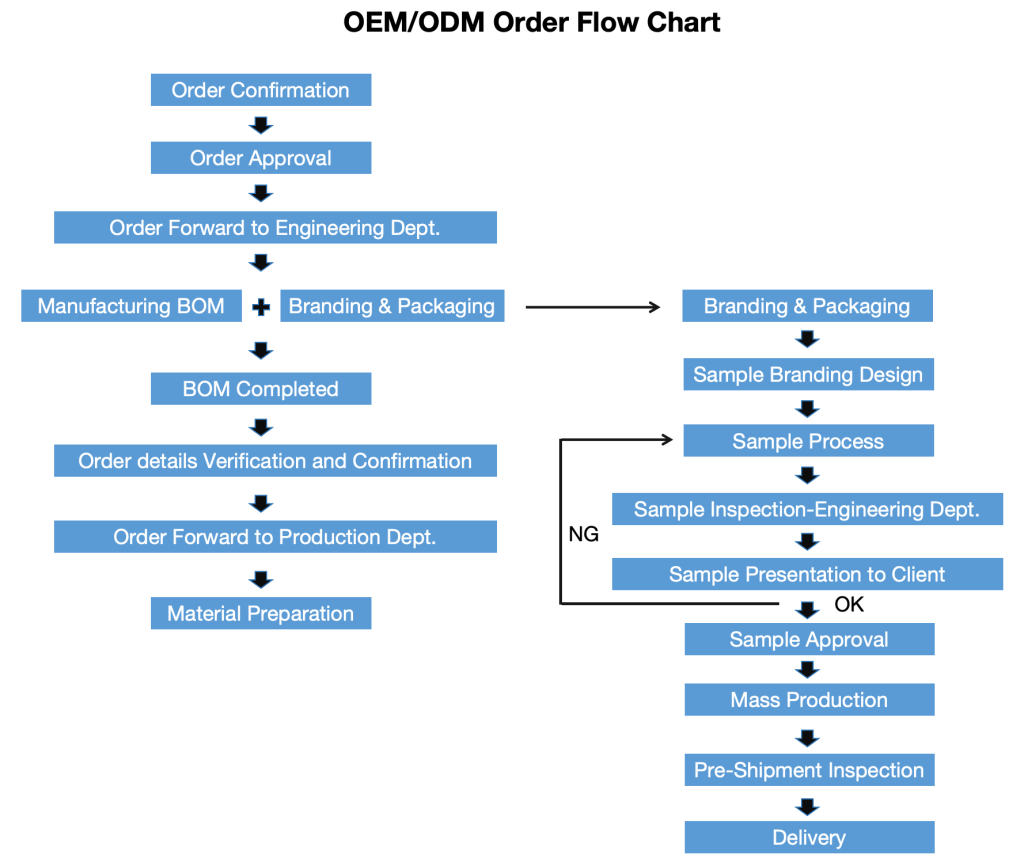
Common logo Techniques
In the process of OEM orders, there are various methods for creating logos on products, each with different application scenarios, effects, costs, and production speeds. Below is a summary of several common methods and their comparisons:
1. Silk Screen Printing
Principle: Ink is transferred onto the product surface through a silk screen stencil.
Advantages:
a) Low cost, suitable for large quantity order.
b) Rich colors with strong coverage.
c) Suitable for flat or simple curved surfaces (such as plastic, paper, T-shirts, etc.).
Disadvantages:
a) Not suitable for complex curved surfaces or high-precision patterns.
b) Limited number of colors (color separation and stencil making required).
2. Hot Stamping (Thermal Transfer)
Principle: A heated metal mold transfers the hot stamping foil onto the product surface.
Advantages:
a) High-end effects (such as metallic colors, holographic effects).
b) Wear-resistant and corrosion-resistant, suitable for long-term use.
c) Suitable for plastic, leather, paper, etc.
Disadvantages:
a) High mold cost, not cost-effective for small batches.
b) Only applicable to flat or slightly curved surfaces.
c) Color selection is limited to the types of hot stamping foil available.
3. Laser Engraving
Principle: A laser beam ablates the material surface to create the pattern.
Advantages:
a) Permanent marking that cannot be worn away or removed.
b) High precision, suitable for complex patterns or small text.
c) Environmentally friendly with no consumables, suitable for metals, wood, glass, etc.
Disadvantages:
a) Monochrome only (usually the material’s natural color or oxidized color).
b) High equipment cost, slower processing speed.
c) May lack contrast on dark materials.
4. Pad Printing
Principle: Ink is transferred to irregular surfaces using a silicone pad.
Advantages:
a) Suitable for complex curved surfaces (such as spherical or concave/convex surfaces).
b) Can print multi-color patterns.
c) Commonly used for electronics, toys, tools, etc.
Disadvantages:
a) Weaker ink adhesion, prone to wear.
b) High cost for small batches, with frequent stencil changes required.
5. Hydro Transfer Printing
Principle: The pattern is printed on a water transfer film and then transferred to the product surface using water pressure.
Advantages:
a) Can achieve complex patterns.
b) Suitable for irregular curved surfaces.
Disadvantages:
a) Complex process with lower yield.
b) Average wear resistance, requiring a protective coating afterward.
c) High cost.
6. Embossing/Stamping
Principle: A mold is used to press raised or metal layers onto the material surface.
Advantages:
a) Strong three-dimensional effect with a noticeable tactile feel.
b) Suitable for metals, leather, paper.
c) High durability.
Disadvantages:
a) High mold cost, only suitable for large-scale production.
b) Cannot represent complex colors.
7. Digital UV Printing
Principle: UV ink is printed directly and then cured using ultraviolet light.
Advantages:
a) High precision, capable of printing full-color patterns.
b) No stencil required, suitable for small-batch customization.
c) Suitable for metals, glass, plastics, etc.
Disadvantages:
a) Higher cost, average wear resistance.
b) Requires a high degree of surface flatness on the material.
8. 3D Printing
Principle: A three-dimensional logo is formed using additive manufacturing.
Advantages:
a) Can customize complex three-dimensional shapes.
b) Suitable for personalized products (such as gifts, models).
Disadvantages:
a) Extremely high cost, low efficiency.
b) Surface requires post-processing (such as sanding, coloring).
9. Electroplating/Etching
Principle: Patterns are formed on the metal surface using chemical or electrochemical methods.
Advantages:
a) High durability, suitable for harsh environments.
b) High-end appearance (such as stainless steel, titanium alloy).
Disadvantages:
a) Complex process, high cost.
b) Limited to metal materials only.
10. Stickers/Labels
Advantages:
a) Extremely low cost, can be quickly replaced.
b) Suitable for short-term promotions products.
Disadvantages:
Prone to peeling and lifting.
11. Embroidery
Applicable Materials: Textiles (such as clothing, hats, backpacks).
Advantages:
a) Strong three-dimensional effect with a good tactile feel.
b) High durability, washable.
Disadvantages:
a) Limited to soft materials only.
b) High cost for complex patterns.
The selection of a process depends on the product’s material, budget, production quantity, and the desired pattern effect. Usually, when creating a logo for the first time, there is a stencil fee. For example, processes like screen printing and hot stamping involve the creation of screens or molds. These screens or molds incur a one-time cost during the production process, which is the stencil fee. The stencil fee varies depending on the process used.
Why is there a start-up fee for printing?
When we handle OEM orders for our customers, we often encounter that printing factories have MOQ (Minimum Order Quantity) requirements for printing materials. If the order quantity does not meet the MOQ, sometimes a printing start-up fee will be charged. So, why is there an MOQ requirement? Why is there a start-up fee? And why does the unit price decrease as the printing quantity increases?
Before printing, the printing factory needs to conduct a series of preparatory work such as file processing, platemaking, plate changing, plate adjustment, and trial printing. These tasks require the investment of time, labor, and materials. The startup of the printing machine also consumes certain energy, such as electricity and ink. Regardless of the printing quantity, steps like equipment debugging and preheating are necessary after the machine is turned on, all of which incur fixed costs.
When the customer confirms the file and it is necessary to produce CTP plates, one plate is required for each color. Normally, a set of four-color plates consists of four plates, and if there is an additional color, one more plate is needed. The plates are placed in each station of the printing machine, with each station representing one color.Then, the plates are loaded, aligned, ink is adjusted and applied, paper is loaded, trial printing is done, and colors are adjusted on the computer (making them darker or lighter). Each adjustment requires running dozens of sheets of paper. In the end, at least 150 to 200 sheets of paper are wasted for color correction for a set of plates. After a set of plates is used for printing, the CTP plates can only be scrapped as waste. Whether the quantity is large or small, this set of CTP plates is necessary, and the paper used for alignment and the master printer’s color adjustment process are the same. Therefore, printing factories usually set a minimum printing quantity (MOQ). When the printing quantity is larger, the start-up fee is spread over a larger number of units, making the unit price cheaper. Conversely, if the quantity is smaller, the start-up fee distributed to each unit results in a higher unit price. If the initial printing quantity does not meet the MOQ, some printing factories may also charge a setup fee.
With our many years of extensive OEM experience, you can confidently entrust your orders to us. We have the capability to tailor the best solutions for you, ultimately saving you time, energy, and money.